Understanding BOM and Its Role in Manufacturing
Bill of Materials (BOM) is a crucial component in the manufacturing industry, serving as a comprehensive list of all the materials, components, and sub-assemblies required to produce a product. In this article, we will delve into the intricacies of BOM, its various types, and its significance in the manufacturing process.
What is BOM?
The BOM is essentially a detailed inventory of all the parts and materials needed to manufacture a product. It provides a clear and structured overview of the product’s components, their quantities, and their relationships. By using a BOM, manufacturers can ensure that they have all the necessary materials on hand to produce the product efficiently and accurately.
Types of BOM
There are several types of BOMs, each serving a specific purpose in the manufacturing process:
Type of BOM | Description |
---|---|
Engineering BOM (EBOM) | Used for product design and engineering, providing a detailed description of the product’s components and their relationships. |
Manufacturing BOM (MBOM) | Used for production planning and execution, containing information about the materials, components, and sub-assemblies required for manufacturing. |
Procurement BOM | Used for purchasing and supply chain management, providing information about the suppliers and vendors of the required materials and components. |
Service BOM | Used for maintenance and repair, providing information about the parts and components required to service the product. |
Benefits of BOM
Implementing a BOM in the manufacturing process offers several benefits:
-
Improved efficiency: By having a clear and structured list of materials and components, manufacturers can streamline their production process and reduce waste.
-
Cost savings: A well-managed BOM can help manufacturers identify cost-saving opportunities, such as sourcing materials from lower-cost suppliers or reducing the number of components needed.
-
Enhanced quality control: A BOM ensures that all the necessary components are used in the manufacturing process, reducing the risk of defects and improving product quality.
-
Improved communication: A BOM serves as a common language between different departments within a manufacturing company, facilitating better communication and collaboration.
Challenges in Managing BOM
While BOMs offer numerous benefits, managing them can be challenging. Some common challenges include:
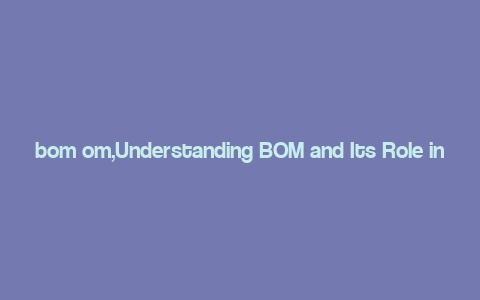
-
Complexity: As products become more complex, their BOMs can become increasingly intricate, making it difficult to manage and maintain.
-
Version control: Ensuring that all stakeholders have access to the most up-to-date BOM version can be challenging, especially in large organizations.
-
Data accuracy: Ensuring that the BOM data is accurate and up-to-date is crucial for the success of the manufacturing process.
Best Practices for Managing BOM
Here are some best practices for managing BOMs effectively:
-
Use a centralized BOM management system: A centralized system ensures that all stakeholders have access to the most up-to-date BOM information.
-
Implement version control: Use a version control system to track changes to the BOM and ensure that all stakeholders are working with the latest version.
-
Regularly review and update the BOM: Regularly review the BOM to ensure that it is accurate and up-to-date, and make necessary updates as needed.
-
Train employees: Provide training to employees on how to use the BOM management system and the importance of maintaining accurate and up-to-date BOM data.
Conclusion
BOM is a critical component in the manufacturing process, providing a comprehensive list of all the materials, components, and sub-assemblies required to produce a product. By effectively managing BOMs, manufacturers can improve efficiency, reduce costs, and enhance product quality.